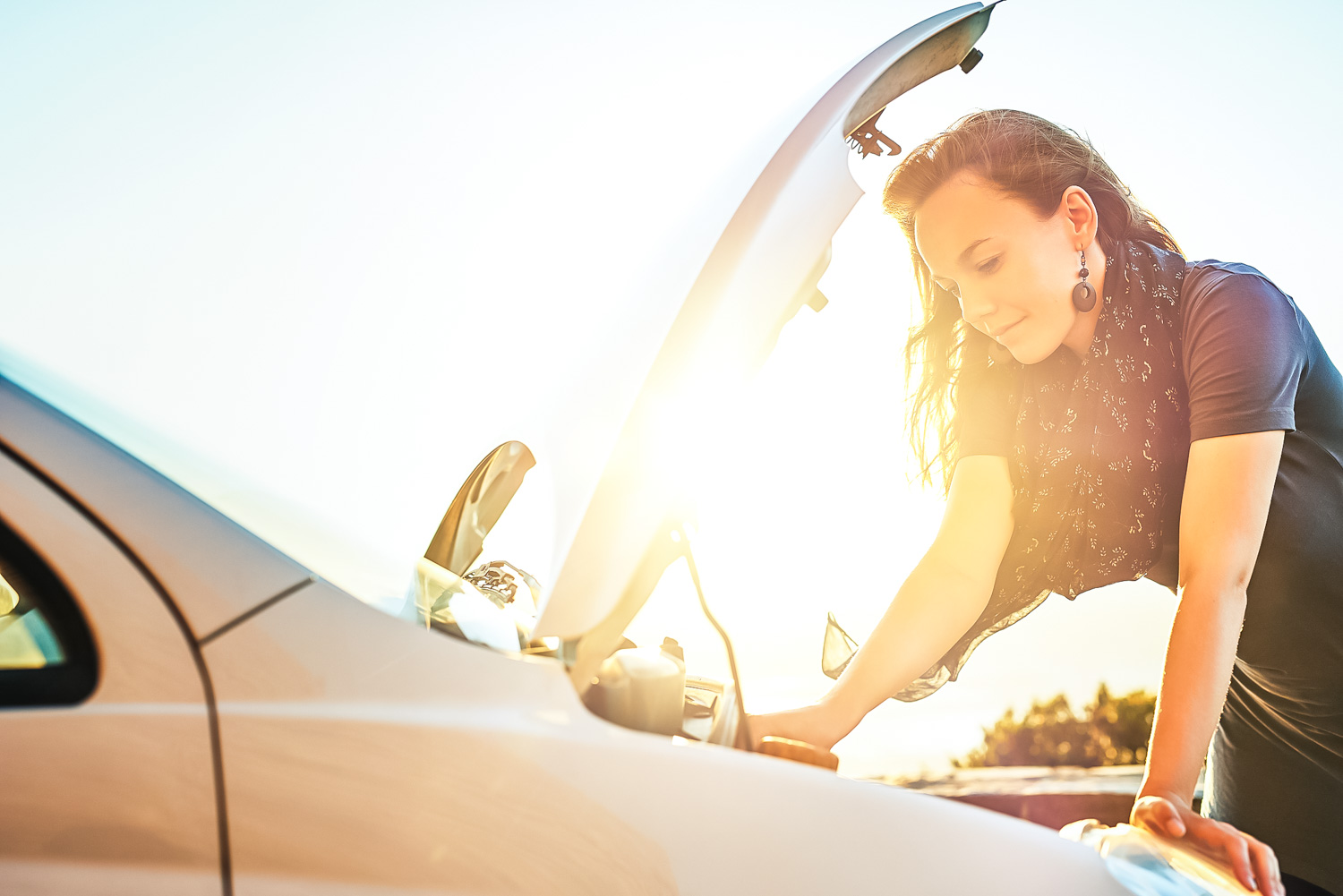
The COVID-19 pandemic may have caused you to park some of your fleet vehicles for the last several months. And if you’re now considering putting them back on the road, there are some mechanical issues that need addressing first.
Taking the steps to ensure a parked vehicle is ready for service again will help you prevent costly repairs and even accidents. So in today’s article, we’ll give you some simple tips for inspecting your idle vehicles and share our own process for helping our clients get their vehicles back in action.
We’ll also share some important information to be aware of regarding vehicle parts shortages and how maintenance service centers and dealerships may be operating differently during this time.
Start by inspecting your vehicles with these 5 steps
1. Check for leaks around the vehicle
Walk around the vehicle and check underneath to see if any fluids have been leaking. If you notice any, call a professional to help determine their cause.
If you don’t see any evidence of leaks, move on to the next steps.
2. Inspect the engine oil
Use the vehicle’s dipstick to check the oil level, which should lie between the dipstick’s two indicator marks. Be sure to check the oil’s colour and consistency as well. If it’s thick, gritty, and dark, it’s time for an oil change.
3. Check all fluids
Make sure the coolant and brake fluids are filled to their required levels. If the brake fluid is low or dirty, it could indicate serious problems that you’ll need a professional to help resolve.
4. Check the battery
Since idle batteries lose voltage over time, you may not have the power you need to start your vehicle. One way to avoid this is to plug your vehicle into a trickle charger if you know it won’t be used for a while. You should also ensure batteries have a full charge and are disconnected from the engine before initially parking a vehicle.
To check your battery health now, simply turn your vehicle’s ignition as you normally would and see if it starts. If not, you’ll need to perform a boost, but make sure to first remove the battery cables and check that the terminals are free of corrosion and debris. If the vehicle still doesn’t start, call a professional for help.
5. Check the fuel quality
Gas that’s been in your vehicle’s tank for a month or longer will start to break down, which could lead to an engine stall while driving. If your vehicle’s been parked for one-to-two months, top up the fuel tank with new fuel before driving anywhere. If it’s been sitting for three months or longer, contact a professional to drain the tank and fill it with fresh fuel.
Check out: Four Ways to Maintain Your Fleet Vehicles When They’re Not In Use.
What to do if your vehicle needs extra help
After completing the above steps, you may realize you need the help of a professional mechanic to get your vehicle running safely and smoothly again. In this section, we’ll explain the process we have here at Foss National Leasing for getting our clients’ idle vehicles road-ready again.
If a driver calls us about a vehicle that won’t start, we identify the driver’s location and then send Roadside Assistance out to boost the vehicle. If it doesn’t start, we have it towed to the appropriate dealership or independent shop for inspection. We have long-standing relationships with a number of reputable vendors, and we always send our clients’ vehicles to people we trust.
After delivering an idle vehicle to a technician, we let them know how long it’s been sitting for. Any vehicle that’s been parked for more than three months will likely need a thorough inspection. For example, brake rotors can begin to rust when not in use, especially if the vehicle’s been sitting in a more humid climate.
After the technician provides us with the cost estimate, we give them the go-ahead to start the work, as long as the estimate doesn’t exceed our authorized limit. If the cost is greater than our limit, we call the fleet manager for authorization.
The technician will then get to work on the needed repairs, preparing the vehicle to get back on the road as soon as possible.
And don’t forget, as part of our maintenance program, you get access to a number of service centres, such as Canadian Tire, that have great service packages available, with convenient hours.
Important things to keep in mind when seeking vehicle maintenance help
Parts shortages are affecting maintenance
It’s important to be aware of how the global parts shortage may affect any vehicle maintenance you need right now. While there are no guarantees, we at Foss are working hard to engage our vendors in an effort to get the parts that we need. We follow up with them regularly, to get the most accurate ETA for any required parts.
Additionally, dealerships and service shops are already considering aftermarket parts and trying to find alternate solutions for parts that their customers need.
Service centers are operating differently
Since many dealerships and service centers still have not gone back to original operating hours due to Covid-19, it’s important to call or email ahead of time to make an appointment. The last thing you want is to show up, thinking you can bring a vehicle in for repairs, and realize they now close three hours earlier than is stated on their website.
And while the rollout of vaccines is improving the situation, some service centers or dealerships may have to shut down suddenly if a staff member is exposed to Covid-19. This can be extremely frustrating for a business that has a vehicle in the shop waiting for repairs. And while the frustration is understandable, these incidents can happen, so it’s best to be aware and have a backup plan if you find yourself in this situation.
Final Thoughts
Getting your idle vehicles ready for service again is a great issue to have, because it means business is picking up. Use the five steps we’ve outlined above to do a quick initial inspection. And if you find your vehicles need more in-depth care, don’t hesitate to reach out to a reputable technician. Finally, be aware that Covid-19 is affecting which vehicle parts are available and how service centers are operating right now, so plan ahead where you can.
Get to Know the Author
After having worked with Foss National Leasing part-time while attending Brock University, in 1995 Lori graduated and began her full-time fleet career at Foss.
Starting in Purchasing, moving to Client Services and then on to Operations, she has worked her way up alongside some great mentors and leaders, becoming a key member of the Management Team.
As Director of Card Operations, Lori is responsible for our suite of fuel and maintenance card products. Lori works in unison with the Technology and Business teams to continually improve the features of the card offerings. Some of the projects she was directly involved in include the development of our PIN technology and Fuel Exception Reporting – both of which were a Canadian first in our industry.
As a cancer survivor, Lori has a new lease on life and enjoys spending all of her spare time with her family and friends on the water, sitting around a campfire, and travelling.
Meet our team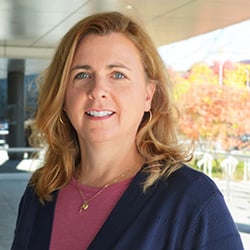